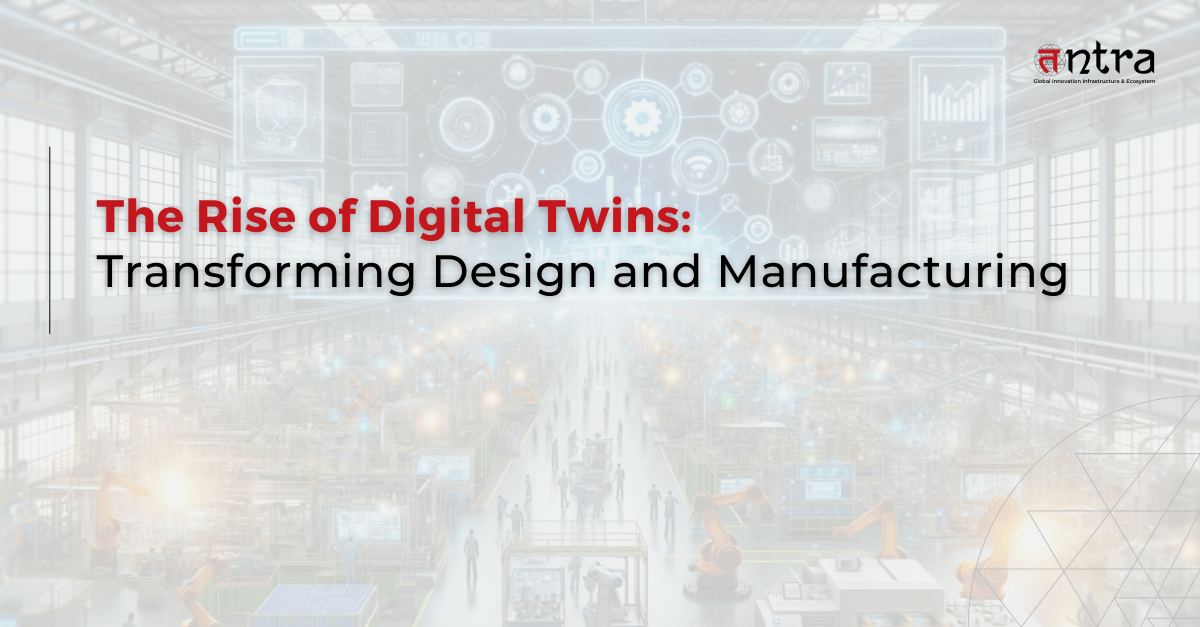
The Rise of Digital Twins: Transforming Design and Manufacturing
Table of Contents
ToggleArtificial intelligence, analytics, and computing power developments are directly responsible for the rise of digital twins. Digital twins are virtual replicas of current or future products that can replicate every detail of their physical equivalents. Manufacturers make decisions and update their digital twins based on real-time data by using simulation and machine learning. Digital twins are simulations and studies with varying degrees of complexity, ranging from one to several dimensions. They can be used in a wide range of engineering and design domains, including fluids, structures, and signal integrity. Continue reading to learn more.
Rolls-Royce, a multinational aerospace and defense firm, uses digital twin technology to track the engines it manufactures. The operator has the ability to track each engine’s flight characteristics, pilot usage, and flying conditions.
Stuart Hughes, chief information and digital officer of Rolls-Royce, says, “We’re tailoring our maintenance regimes to make sure that we’re optimizing for the life an engine has, not the life the manual says it should have.” “The service is genuinely variable, treating each engine as a standalone unit.”
Although Rolls-Royce has always provided engine monitoring to its clients, its capacity to create digital twins has allowed the corporation to customize the service for certain engines. It has allowed the corporation to significantly reduce its inventory of parts and spares by extending the interval between maintenance for some engines by up to 50%. By increasing the engine efficiency, technology has also allowed Rolls-Royce to save 22 million tonnes of carbon to far.
With assistance from Accenture’s digital manufacturing and operations consultants, Mars is utilizing Microsoft’s Azure Digital Twins IoT technology to enhance operations throughout its 160 production locations. The organization is developing software simulations to enhance capacity and process controls. These include lowering waste related to machines packaging uneven product volumes and increasing machine uptime through predictive maintenance. Mars may also create a virtual “app store of use cases” that can be used to other business lines by utilizing the digital twin concept.
(Source: CIO)
The Rise of Digital Twin Technology
The market for digital twins is expected to reach a valuation of USD 16.75 billion globally by 2023, and it is anticipated to expand at a compound annual growth rate (CAGR) of 35.7% between 2024 and 2030. The ability of digital twin technology to close the gap between the real and virtual worlds is why it is becoming more and more popular.
According to a 2023 poll conducted among 750 CFOs at large corporations worldwide, digital twin technology was utilized by approximately 15% of real estate organizations. About 22% of executives stated that their company was still in the early stages of adopting the technology, while 30% were really testing it out.
How Digital Twins Reshape Manufacturing and Design
Building on developments in artificial intelligence, analytics techniques, and processing capacity, digital product development methodologies are also growing quickly. The result of these is the rise of digital twins, which are virtual copies of existing or upcoming items that may mimic every feature of their real-world equivalents. In comparison to real-world interactions, interacting with or altering a product virtually can be quicker, simpler, and safer.
Manufacturers use machine learning and simulation to make judgements and update their digital twins based on real-time data. The twins are analyses and simulations, varying in complexity from one-dimensional to multi-dimensional. They are applicable to many different engineering and design fields, such as signal integrity, fluids, and structures.
In order to increase manufacturing efficiency, manufacturers monitor production lines and other processes using virtual duplicates of equipment made of digital twins and threads. Digital twins monitor pressure, temperature, speed, and other external factors in addition to critical performance parameters. Businesses can use the data to promptly identify and track any production line irregularities that might point to a potential problem or flaw.
The adoption of digital twins and digital threads by manufacturers is happening faster and faster. By going virtual, they can assess data, boost productivity, and streamline processes. Industrial processes can be digitally replicated to enable speedy data assessment, performance trend analysis, and operational optimisation before expensive malfunctions occur. Product reliability is increased and downtime is decreased by the quick response capabilities.
These businesses, along with other trailblazers in the digital twin space, have four primary reasons for investing in the technology.
- Design and engineering teams can investigate additional design choices with digital twins since they offer a risk-free environment for product development, eliminating the need to pay for the creation and testing of physical prototypes.
- By enabling the evaluation of novel solutions in a variety of realistic settings, including uncommon and harsh operating circumstances, digital twins enhance testing and validation.
- Digital twins provide better information into product behavior. Digital-twin models allow engineers to trace intricate relationships between product elements and monitor the status of every component of the system at any given time.
- Through the use of digital twins, which simulate the effects of suggested design modifications using data gathered from items in use, real-world data can be used to inform product enhancements.
Benefits of Digital Twins in Manufacturing
- Design and prototyping
Manufacturers can virtually duplicate machine tools prior to their physical fabrication with the use of digital twin technology. This makes it possible to test and prototype in a virtual setting, giving engineers the chance to identify and resolve possible problems prior to the start of real production.
- Tracking of performance
Maintaining efficiency and lowering unplanned downtime require careful attention to machine tool performance monitoring. Manufacturers can track its performance parameters continually thanks to digital twin technology. Proactive monitoring reduces the likelihood of costly breakdowns by identifying problems early on and enabling predictive maintenance procedures.
- Increased effectiveness of production
Through the provision of insights into the interactions between various parts of the manufacturing ecosystem, digital twin technology aids in the improvement of production processes. This entails keeping an eye on production output and machine utilization, among other things. This increases overall efficiency, breaks down bottlenecks, and optimizes processes, which raises productivity and lowers operating expenses.
- Accuracy and assurance of quality
Accurate machining process analysis and simulation are made possible by digital twin technology. This results in items of the highest caliber. This lowers expenses in addition to improving precision.
Final Thoughts
To increase performance, digital transformation mainly uses digital tools for plant and product development. Usually, digital transformation initiatives fit into one of two groups.
Moving from fragmented, compartmentalized representations of products and plants to a holistic digital twin is the emphasis of one type of digital transformation. A different course focuses on replacing manual tasks and procedures that depend on electronic and hardcopy artifacts with more advanced automated digital threads.
Tntra, a software product engineering company has experts in digital twin technology who can replicate and stimulate real-word scenarios to improve your business cases. Schedule a call with them and get started on your digital twin journey today!