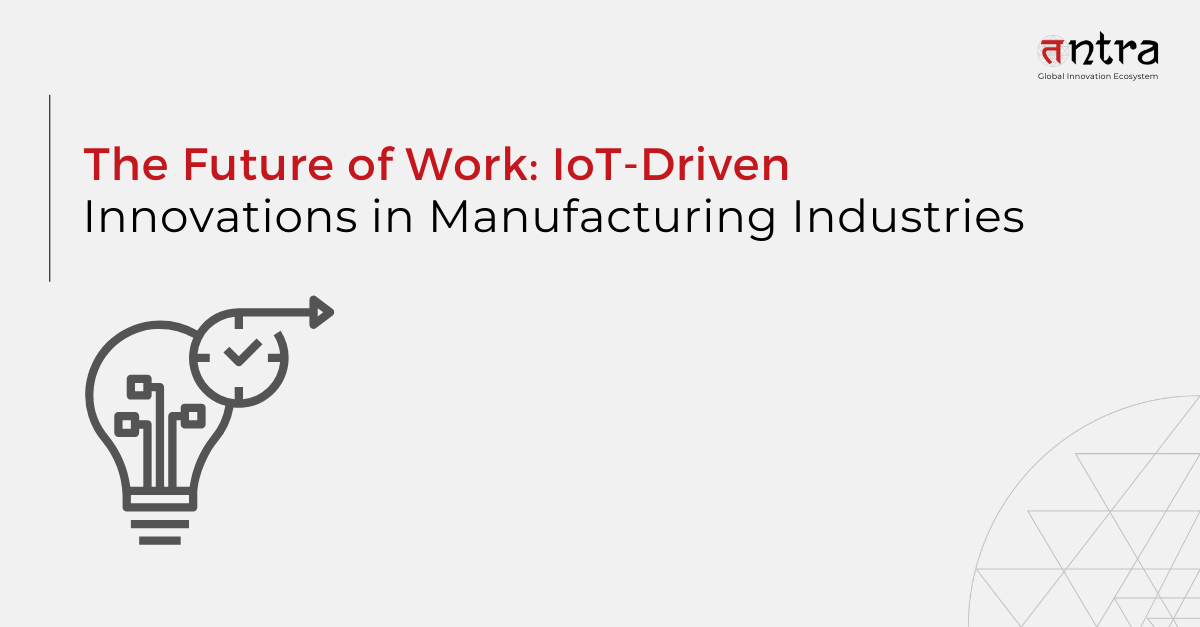
The Future of Work: IoT-Driven Innovations in Manufacturing Industries
Table of Contents
ToggleIoT in the manufacturing industry is changing the manufacturing Future of Work. IoT-powered data-driven insights, predictive maintenance, and improved warehouse management are transforming the manufacturing industry. Through integration, it guarantees safety, effective operations, and well-informed decision-making, converting manufacturing into an environment where IoT is a strategic asset rather than merely a tool. IoT software development services like Tntra, an IoT application development business that represents the future of industrial excellence through innovation and technological integration, spearheaded this revolutionary change.
According to General Electric (GE), technology advancements, particularly in IoT manufacturing solutions, will fuel a vibrant Future of Work. As a leader in digital innovations designed for the industrial environment, GE Digital is a key player in transforming traditional work models.
GE recognizes that an IoT solution for the manufacturing process can revolutionize the industry and that this potential is already a reality. Their continuous commitment to innovation has resulted in Predix, a specialized platform that optimizes the asset lifetime. This embodies GE’s dedication to digitally developing the industrial sector by enabling industries to increase operational efficiency and make better-informed decisions.
Their strategy is based on learning alongside clients, as demonstrated by partnerships with large organizations such as Exelon, BP, and Qantas. These collaborations produce measurable results by utilizing Predix-based solutions, confirming GE’s leadership in the IIoT space.
Despite obstacles, GE is still well-positioned for future success. They strongly emphasize competition in the rapidly changing IIoT market and the continuous search for top talent. GE’s unique approach to measuring success, which centers on distinct product offerings and well-defined growth targets, demonstrates their commitment to successfully navigating an unexplored market.
GE Digital is positioned for success with a strong focus on personnel retention and a strong leadership culture. Their steadfast dedication to leveraging IIoT advancements to empower industries displays a vision and a strategy roadmap toward long-term leadership in the rapidly changing Future of Work.
Source: General Electrics
Transformative Trends: The Evolution of IoT in Manufacturing
A stable compound annual growth rate (CAGR) of 11.9% is predicted for the Manufacturing IoT market, which was valued at $50.0 billion in 2021 and is expected to reach roughly $87.9 billion by 2026.
An industrial assessment from 2016 predicted that by 2025, over 75 billion devices would be connected through IoT technology. This exponential rise is more than just a figure; it represents a revolution in the industrial industry. IoT industry solutions facilitate predictive maintenance, streamline factory management procedures, improve efficiency, support quality control measures, and optimize processes.
IoT in the manufacturing industry is expected to reach USD 200.3 billion by 2030, a phenomenal 13.9 percent compound annual growth rate from 2021. This trend demonstrates how crucial IoT is to transforming the way industries function and prosper.
In a 2019 Deloitte poll of executives in the manufacturing sector, 86% of respondents said IoT in manufacturing — specifically, smart factory initiatives — would be the industry’s driving force over the next five years. Interestingly, at the time of the poll, just 51% of these CEOs had invested in this field.
IoT Empowering Operational Efficiency in Manufacturing
Digitization is driving a radical transformation in the manufacturing sector. Businesses use innovative technology to transform their surroundings. The industry constantly strives to increase efficiency and reduce expenses through streamlined operations, and Internet of Things (IoT) solutions have shown great potential in this regard.
The research indicates that leaders in the industry are inclined to implement innovative Industry 4.0 solutions. These days, the stories of digital successes are powerful catalysts for adopting an IoT-based solution.
- Predictive Maintenance
In the dynamic manufacturing landscape, unforeseen downtime poses financial risks. It threatens worker safety. IoT in the manufacturing industry, facilitated by IoT development services, introduces sensors monitoring variables like temperature and vibration. These sensors act as early warning systems, predicting malfunctions and ensuring workplace safety.
Manufacturers reduce expenses associated with subpar quality by proactively preventing equipment failures through IoT-enabled predictive maintenance. These IoT wireless sensors forecast downtime, identify possible faults, and evaluate the health of the equipment. They protect against production disruptions by monitoring machinery vibrations and forecasting potentially dangerous situations, enhancing operational safety in manufacturing settings. Integration of IoT provides a proactive barrier, preventing interruptions and enhancing safety throughout production lines.
- Quality and Safety
IoT sensors collect various data throughout the product cycle, including input from third parties. This allows manufacturers to distinguish between items that satisfy quality standards and those that require physical inspection. When combined, this data covers the composition of raw materials, the effects of transportation, and even customer feedback.
These kinds of insights help identify and address quality problems. However, the benefit of IoT in the manufacturing industry is mostly in secure data management. This enables smooth device-to-device connectivity and helps proactive manufacturers beat the competition.
- IoT Data
IoT data is a very useful resource that appears in the world of IoT devices and networked systems. Beyond its mere size, its value is in providing insights and facilitating data-driven decision-making in the context of Industry 4.0’s manufacturing transformation. IoT data has enormous promise since it provides detailed insights into system performance, equipment behavior, and processes.
Beyond just numbers, its importance lies in its ability to support trend forecasting, anomaly detection, and pattern recognition. Data is no longer just a commodity in today’s world; it is a strategic asset, and IoT data, with its real-time depth, is the basis of this transformative age. Its uses include quality assurance, supply chain optimization, predictive maintenance, and improved customer experiences.
- IoT in Warehouse Management
Within manufacturing, logistics reigns as a critical facet, demanding substantial investments for enhanced management. IoT sensors play a pivotal role in positioning manufacturers ahead by ensuring preparedness for unforeseen events.
Warehouse management grapples with storing vast product volumes, expediting order processing, efficient inventory tracking, and escalating transportation expenses. IoT applications in manufacturing empower proactive solutions, addressing these challenges head-on and optimizing operations to navigate the complexities of logistics efficiently.
Dive into our case study to see how Tntra transformed a plastic injection molding company with real-time IoT monitoring solution: Read the success story now!
Conclusion
The trajectory of IoT in the manufacturing sector signifies an imminent revolution in the Future of Work. From predictive maintenance to quality assurance and streamlined warehouse management, IoT applications wield a transformative power, amplifying operational efficiency and safety protocols.
Companies of many sizes see the revolutionary potential of IoT manufacturing. By anticipating problems and guaranteeing worker safety, its integration enables preventative measures. Integrating IoT data facilitates well-informed decision-making and optimizes supply chains and systems. IoT is now a strategic asset influencing operational excellence in manufacturing, not merely a tool.
IoT data integration into manufacturing processes drives the sector toward better decision-making, supply chain, system, and process optimization. IoT technology is clearly becoming more than just a tool for manufacturing; rather, it is a strategic asset defining a new era of operational excellence.
This revolutionary change, brought about by IoT integration in the manufacturing sector, emphasizes how certain it is that the Future of Work will undergo a paradigm shift. This new era of IoT as the cornerstone influencing the future of manufacturing rather than merely a technical tool has been marked by seamless connectivity, proactive solutions, and data-driven initiatives. The widespread impact of an IoT application development company like Tntra is recalibrating the fundamental nature of work in manufacturing as they continue to innovate.
Tntra is a leading software product engineering company that strongly focuses on New Economy technologies, including IoT.
Contact IoT experts at Tntra today and take your manufacturing excellence to the next level.